Vol.1 DX/時系列データ分析の課題
はじめに
いま、電力・製造業界全体で「データを活用した経営及び生産現場の意思決定」に関する注目度が高まっています。この記事をご覧いただいている皆様の中にも、分析技術や機械学習を効率的に使いこなして生産効率を高めたいという問題意識を持たれている方が多いのではないかと思っています。
背景には、近年IoT技術の発展に伴い工場設備等から大量のデータを時系列に収集・蓄積できるようになったことがあります。工場設備等から取得されたこうした時系列データの分析結果は、故障の予兆検知等、業務効率化に活用することができます。しかし例えば取得したデータをそのまま分析してもうまくいかない等、データの利用にあたっては考慮しなければならない点も多くDXを進めていく上での課題になっています。
そこで、今回のMKIナレッジでは、現場の業務効率化を実現し、企業の収益を高める為のデータ活用(=分析の高度化)とその課題について説明します。
時系列データを活用したDXに対する期待
まず初めに、私たちを取り巻く時系列データを活用したDXに関する経営からの期待・それを取り巻く技術動向について振り返ります。
先ほども触れました通り、ここ数年、新しいハードウェアが誕生し、私たちDXを推進する担当者はセンサーやIoTデバイスを通じて、工場内の様々な種類のデータを収集できるようになってきました。
次に、データを蓄積するソフトウェアついても、PI Systemをはじめとするヒストリアン、アマゾン ウェブ サービス(AWS)をはじめとするクラウド、各種メーカーが提供するクラウド型のIoTプラットフォーム等、様々な選択肢が増えました。結果として、データを保存するコストもかなり削減できるようになってきました。
コストが下がってきたというのは非常に重要な要素で、本社にDX推進部門を組成して、各工場単位で管理されていたデータを統合して新たなインサイトを発見していこうという機運を後押ししています。
こうした状況の変化により、DX推進部門には、蓄積したビックデータを利用してより深いインサイトに繋げてほしいという大きな期待を経営層からよせられプロジェクトをスタートした方や、まさにこれから始めようとDX推進部門への参画を要請された方も多くなっています。
DX推進で直面する3つの課題
しかし、残念なことに、この分野のデータ分析についてはお悩みを抱えている方が多いのが現実です。既にプロジェクトをスタートされている方は、単にデータを集めて分析しただけでは、より深いインサイトに繋げるのは難しいと感じているのではないでしょうか?
私もDXの担当者として、時系列データを活用した様々なデータ分析を実施してきましたが、他テーマのデータ分析等と比較すると電力・製造業におけるデータ分析には考慮するべき点が多くあると考えています。こう感じた理由を業務のポイント毎に説明します。
① データの収集と補完
② PDCAを回す際の社内専門家からのフィードバック
③ リアルタイムに近い状態で分析結果を社内関係者と共有
時系列データは分析に向いているきれいなデータとして保存されているケースは非常に稀です。また、工場担当者はデータタグを見てそのデータが何のデータかをすぐに理解できますが、分析を担当するDX担当者には理解できない場合も多いです。加えて、DX担当者は受領したデータがデータクレンジングをしないと分析に使えないという問題に直面します。
データ収集と補完が終わった後で、DX担当者が分析を開始します。この時、社内の専門家からフィードバックを受ける体制がないために、誤解の生じやすい分析結果を導き出してしまうケースがあります。例えば、あるセンサーの数値が3時間ほど乱れていたという場合、実際は現場の判断でその機器をメンテナンスしていたのにも関わらずDX担当者はセンサーの故障と判断して分析をしてしまったというようなケースです。
分析が終わった後は、分析の社内利用に進みます。この時、データ分析結果から様々な解釈が生まれます。解釈に迷いの生じる分析結果・納得感がある分析ロジックが説明できない結果は、残念ながら業務で活用される可能性が低くなります。こうした課題を乗り越えて社内の関係者に見たいと思わせるデータ分析結果を継続的に提案していくことが、DX担当者には求められています。
これに加えて、DX担当者は、データ分析を直ぐにやってほしいという時間的な制約を求められることがあります。そうなると、①から③までの業務を効率的に回して時間的な制約をクリアするために、業務のデジタル化を検討していく必要が出てきます。
DX推進部門が得たいインサイトと課題となりやすいプロセス
時系列データからDX推進部門が導き出したいインサイトについて考えていきたいと思います。得たいインサイトは、以下の5つに集約できると思います。
①何があったのか?
②なぜそれが起こったのか?
③予測と反し、一体今何が起こっているのか?
④どうなるのか?
⑤何が起こるのか?
現場で起こっていることを把握するための工場単位での監視や設備稼働に関する分析(=コア分析)については、多くの企業で工場内のエンジニアが実施しています。DX推進部門に求められる役割は、どちらかというと原因分析だったり、この問題に気が付かなかった場合、他工場に与えるインパクトがあったか等を予測する“アドホックな分析”が中心になっていきます。
DX推進部門が、こうしたアドホックな分析を実施していくと次のような課題に直面することがあります。
① 工場のデータ参照の権限がない
② データ受け渡しの負荷が高い
③ 分析の負荷がかかる
④ BIやAI活用のためのデータクレンジング業務が新たに発生する。
加えて、繰り返しになりますが、時系列データがデータ分析に適した形で保管されていることは稀で、新たなデータ分析を実施する都度、データクレンジングが必要となります。これはBIやAIを使う場合でも同様で、BIとAIに適したデータを作成し投入することになります。
そのため、分析業務をマニュアルで行っている場合、一つひとつの分析に非常に多くの手間と時間がかかり、これが企業のDX推進部門が、データ分析基盤を導入したが楽になるどころか仕事が増えたと感じてしまう原因の一つです。結果として、「 やればできるけど時間がかかりすぎるのでやっていない状態」が生み出されてしまいます。
データ分析の業務をデジタル化し、「分析の高度化」に取り込みやすくなることで、DX推進部門の業務効率化が図れるケースはまだまだ埋もれていると考えています。
Vol.2では、PI System等の時系列データを活用した「分析の高度化」について説明したいと思います。
関連ページ
おすすめコラム:
小売業向け要冷制御
関連ソリューション:
IoTデータ管理ソフトウェア「PI System パイシステム」
Seeq ~プロセス製造業向けデータ分析ツール~
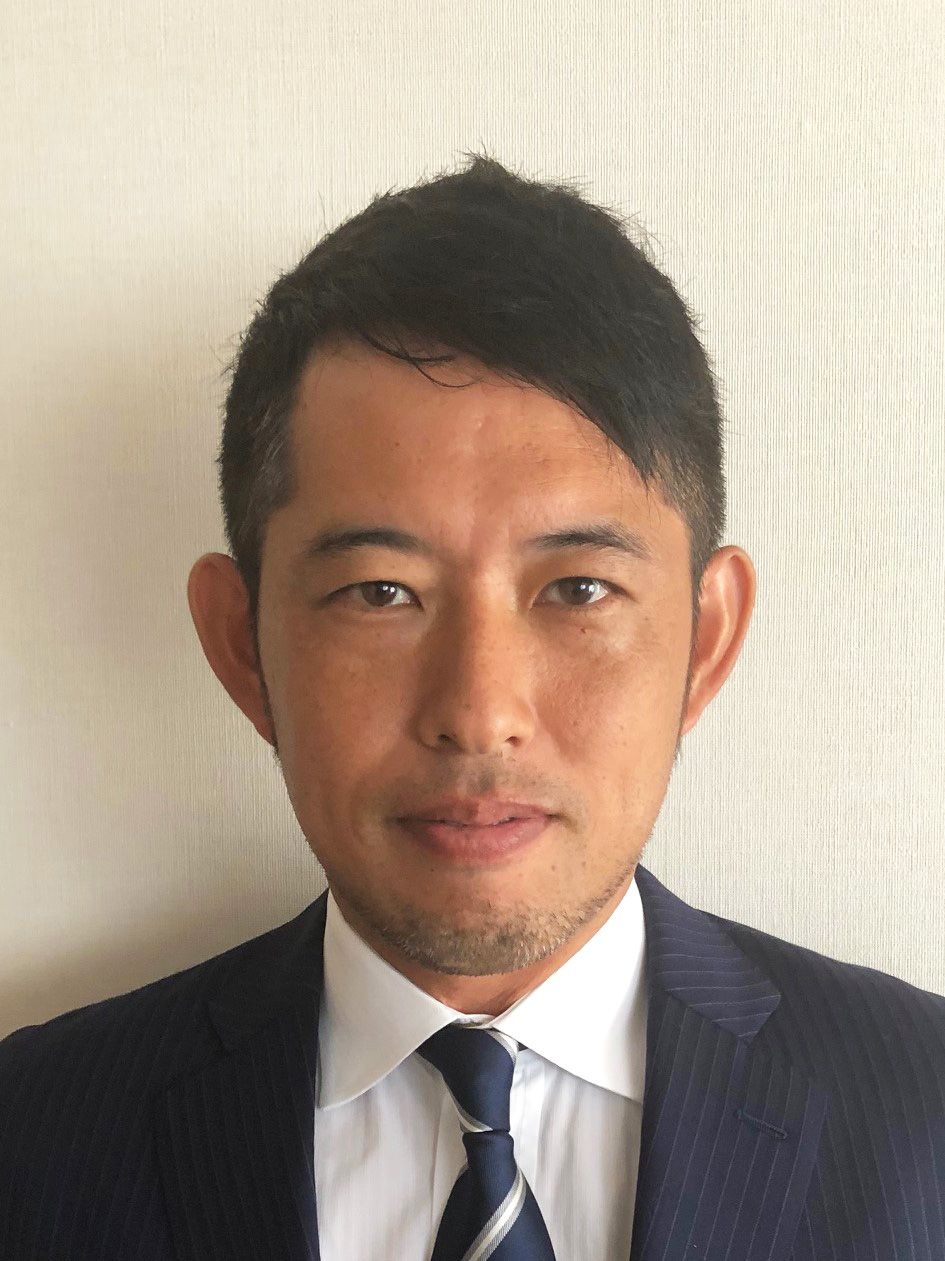
久利生 大輔
デジタルトランスフォーメーションセンター 産業ソリューション営業部 第二営業室
電力・製造業とスポーツ分野でのデータを活用したDXプロジェクトを推進。
コラム本文内に記載されている社名・商品名は、各社の商標または登録商標です。 本文および図表中では商標マークは明記していない場合があります。 当社の公式な発表・見解の発信は、当社ウェブサイト、プレスリリースなどで行っており、当社又は当社社員が本コラムで発信する情報は必ずしも当社の公式発表及び見解を表すものではありません。 また、本コラムのすべての内容は作成日時点でのものであり、予告なく変更される場合があります。